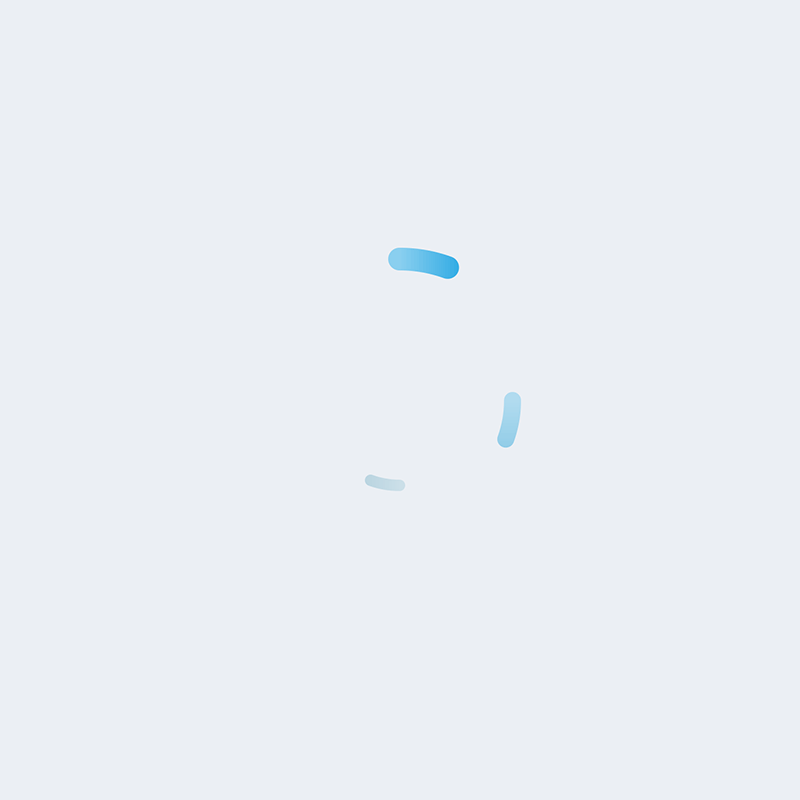
3D Printing in Medical Technology
Additive Manufacturing for Orthopedic Technology
3D Implants and Instruments
With an Optimized Fit and Surface
Patient-Specific and Accurate
Implants and Surgery Instruments From the 3D Printer
EOS additive manufacturing technology creates precisely fitting instruments and implants directly from CAD data.
The process manufactures implants based on anatomical data collected from the wearer and allows them to be delivered quickly. This avoids any waiting times or complications due to extended periods of inactivity, so the implants fit better. It also speeds up the healing process as a whole and has a lasting positive impact on the patient’s quality of life.
Additive manufacturing by EOS can also be used to create a wide variety of surface structures, which can simplify processes such as osseointegration, namely the growth between living bone tissue and the surface of the bone implant. The applications of 3D printed implants include spine implants, shoulder joints (glenoid replacement, hip implants) and implants for the OMF area (oral and maxillofacial surgery).
For complicated interventions, surgeons are increasingly switching to patient-specific single-use instruments. This allows the implants to be inserted more precisely, increasing the success of the operation for patients, surgeons, and hospitals. These customized instruments can also be manufactured with a 3D printer. The surgeon benefits from a high-quality and precise product that meets the strict standards associated with medical applications.
The 3D printed alternative enables greater variety (“mass customization”), and production can be performed “on demand“. Compared to multiple-use instruments, hospitals save on sterilization and storage costs and benefit from higher productivity.
Products can be designed to reflect the diagnosis, no matter their level of complexity, they can be manufactured and delivered to the clinic in the shortest possible time. It takes about 6 weeks for conventional manufacturing, whereas with additive manufacturing, production is possible within just 10 days.
EOS 3D Printing of Implants, Joints & More
Application Examples for Additive Manufacturing
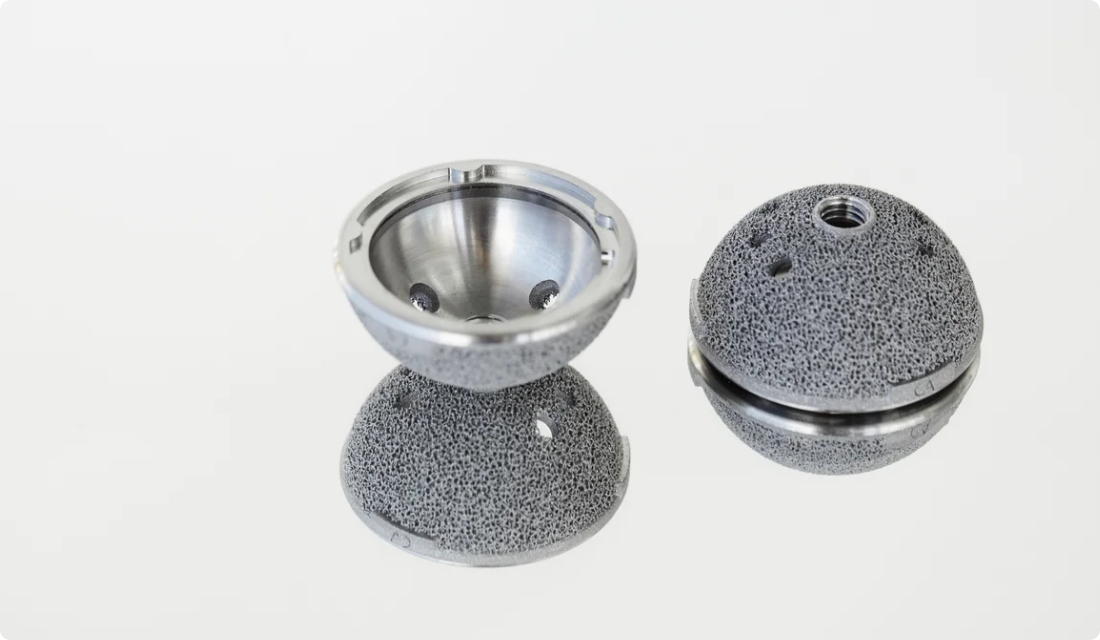
Complex geometries and surfaces of an acetabulum. The filigree structures allow an optimized healing process.
3D Printing in Practice
Permedica: 3D Printing of an Artificial Hip Cup
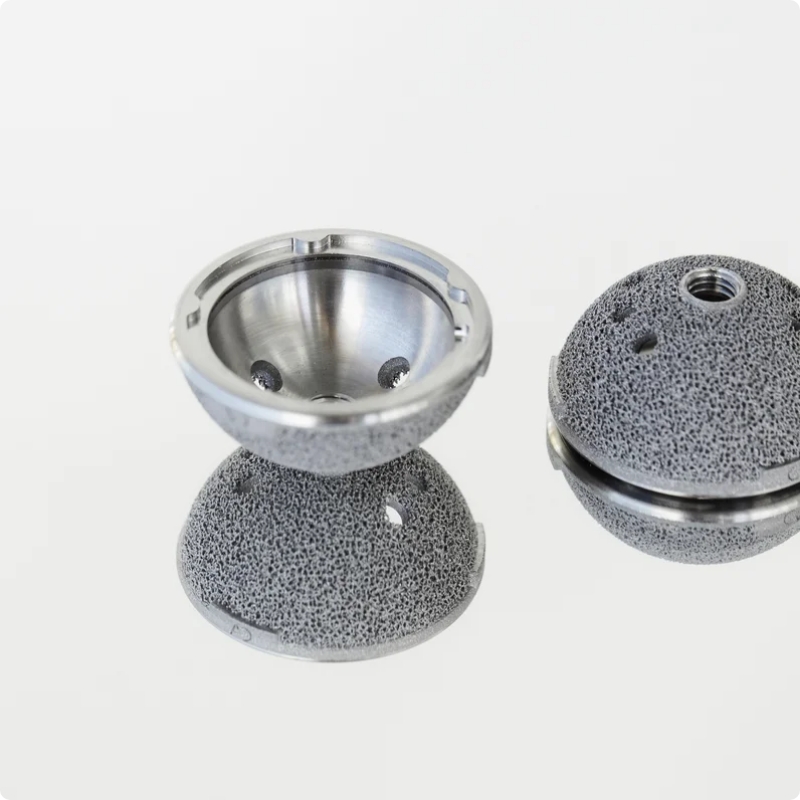
Play video
Surface structure for improved osseointegration
The implant can be significantly optimized thanks to 3D printing. The hip cup consists of fixed sections to provide the necessary stability and elements with rough structures. These elements are structured directly to ensure that the implant is firmly anchored: coarse structures are advantageous in terms of pressure transmission, whereas smaller structures support the initial fixation. In this way, the complex structure simplifies osseointegration, accelerating the healing process.
Flexible production is possible
Together with the EOS Additive Minds team and the well-established EOS M 290 system for metals, Permedica succeeded in creating a completely new product. The entire implant is made in a single production step on the 3D printer and would be incredibly difficult to reproduce with conventional manufacturing methods. Thanks to the high flexibility of additive manufacturing, the surface and size of the hip cup can be specified individually for each patient.
EOS 3D Printing
Additively Manufactured Instruments for Medicine
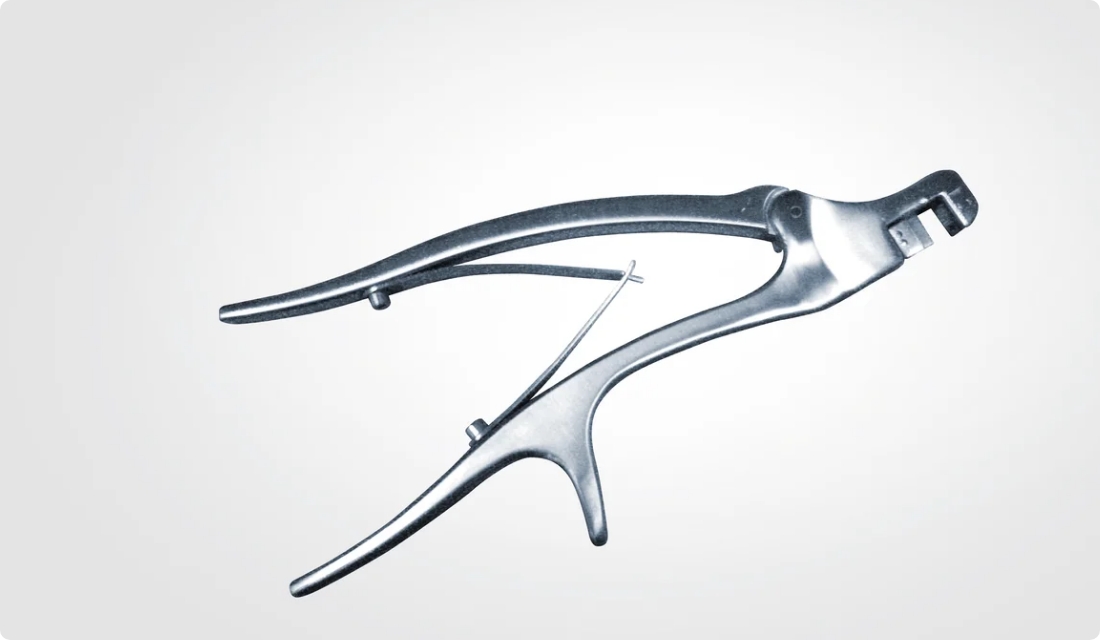
Prototype of a bending instrument to form the plates to be used in spine surgery
Together with BodyCad, EOS developed a surgical drilling template for customized knee arthroplasty. The system offers a more precise and controlled method to prepare the bone for the implant. A combination of a patient-specific implant and a surgical drilling template was developed to facilitate precise knee replacement or restoration interventions that reflect the patient’s anatomical features and musculoskeletal system.
The result was a revolutionary unicompartmental knee system (UKS) with patient-specific surgical instruments. The newly manufactured instruments, featuring custom drilling templates, guarantee higher precision at lower costs, reduced operation times and better clinical results.
Made on an FORMIGA P 110 with the material PA 2201.
-
Efficient
The instruments can be created quickly
-
Profitable
Lower costs compared to conventional processes
-
Timely
Patient-specific instruments can be delivered within 21 days