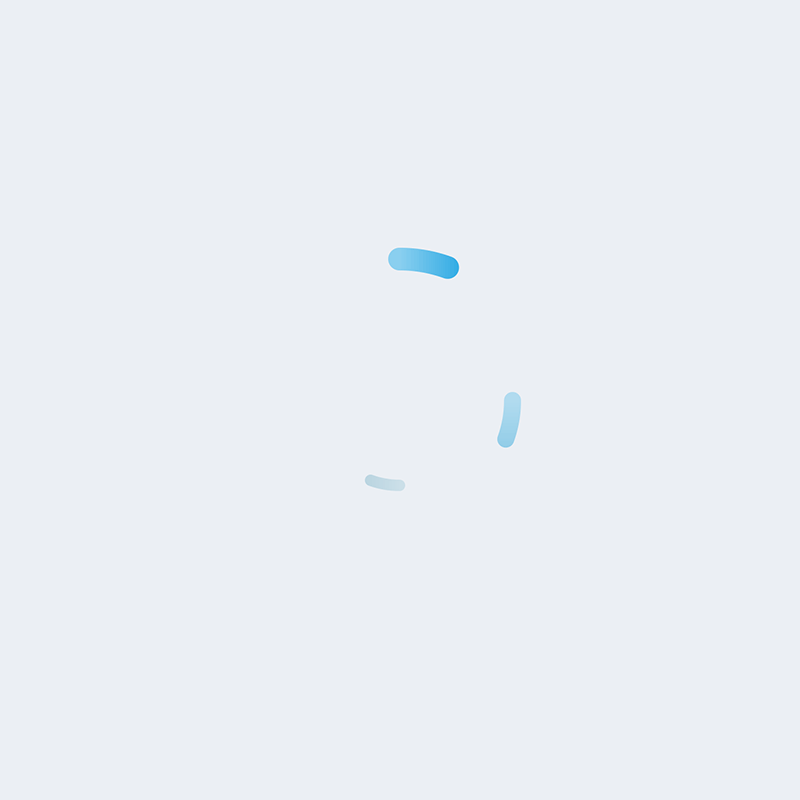
3D Printing in Practice
Housings for Electronic Components
3D Printing as an Efficient Manufacturing Technique
Achieve Favorable Sealing, Dissipation and Stability Properties, as well as Unlimited Shape Diversity
Additive Manufacturing of Plastic Housings
Having a stable housing protects the interior. Robust cases are often essential, especially for sensitive electronics. They need to be strong and properly sealed, while also fitting as closely as possible, and they need to be manufactured quickly enough to achieve short production cycles. However, with the injection molding process, manufacturing housings with these properties is only viable in very large series productions.
Industrial 3D printing offers a cost-efficient alternative for the small and medium series production of plastic housings. Whether made from materials with insulating or especially favorable dissipation properties, the additive manufacturing of housings is characterized by cost efficiency, design freedom and functional integration potential.
Whether you want to make prototypes, pilot series or small series productions of housings, additive manufacturing opens up a great deal of potential – not the least of which being lower production costs.
What Our Customers Have to Say
Statements About Our 3D Printing Technology
When we were examining the costs of 3D printing, we realized that the machine would pay for itself within a year if we used it to manufacture both products. At that point, the right decision was clear.
Mike Schuch | Mech Eng. Manager | Accurate Technologies Inc.
Advantages of Industrial 3D Printing for Manufacturing Housings
-
Extensive design freedom
Making housings with industrial 3D printing gives you more design freedom than conventional processes like injection molding. Rather than being forced to adapt the interior and overall design to fit the housing, our customers can instead adapt the housing to their specific ideas and needs.
-
Rapid innovation capabilities
The electronics and consumer goods markets are characterized by short innovation cycles. Additive manufacturing can prevent waiting times during product development and increase the number of possible iterations for design changes and functional models.
-
Reduced time-to-market
Compared to other processes, products can be placed on the market more quickly. Prototypes, pilot series and series production flow seamlessly into one another. Waiting for plastic injection molds is a thing of the past. The consistency of additive manufacturing processes, from the original idea to the first serially produced parts, turns users into market leaders.
-
Economically attractive manufacturing process
Whether for prototypes or pilot and small series production, industrial 3D printing has a lean cost structure.
-
Simple functional integration
When housings and entire assemblies are made from fewer parts or even in a single piece, they are more stable and robust. Industrial 3D printing makes this possible.
Success Story Canto
3D-Printed Dive Lamp
Canto Ing. GmbH wanted to develop an underwater dive lamp that would be smaller, lighter and more robust than anything else on the market. They succeeded in solving this challenge with an EOS system.
The lamp connection is additively manufactured to allow the internal system, which features a spring latching mechanism, to be produced in a single piece. This allowed the number of assembly parts to be reduced from 3 to 1. Weighing just 580 grams, the lamp is setting new standards. As an added benefit, Canto Ing. GmbH were spared the need to manufacture an expensive injection molding tool, which would have cost up to € 35,000.
The lamp was made manufactured on an FORMIGA P 110 with the material PA 2200.
Find out more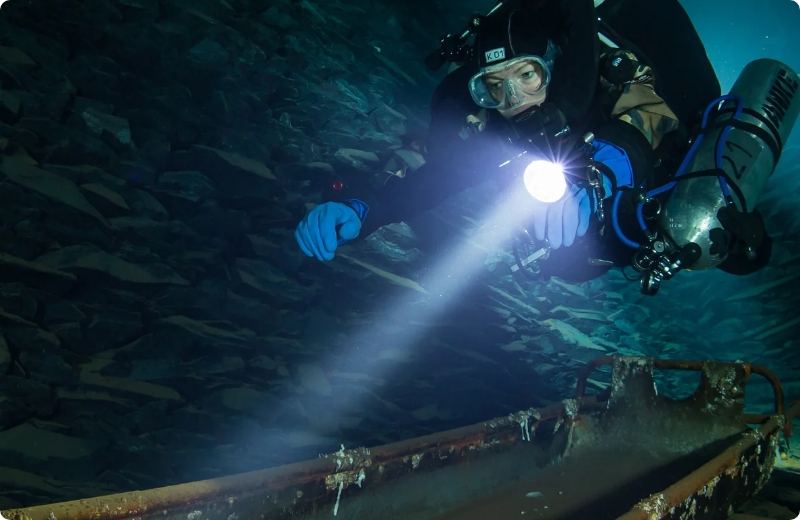
Additive manufactured div lamp by Canto
Success Story
3D Printed Camera Housing for Outdoor Use
Complex Design and Flexible Production
F360 Explorer camera mount
The challenge was to manufacture a low number of units of a robust camera holder with a complex design. The housing needed to be flexible enough to hold six cameras. At the same time, the production process needed to be open to support later design iterations without causing issues.
Thanks to EOS technology, a product design was successfully realized that would previously have been impossible. The partnership with Freedom360 allowed design changes to be made rapidly. Midwest Prototyping were able to implement cost-effective production in small quantities.
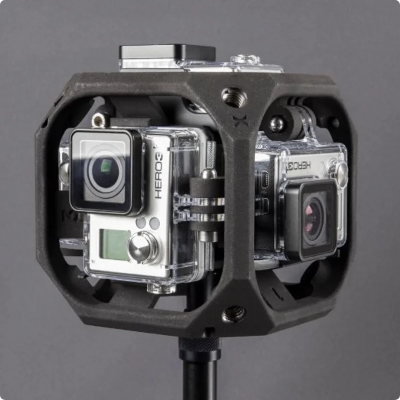
Play video
The Advantages at a Glance
- Innovative product design with structures that would previously have been impossible to manufacture
- Responsive, customizable production with maximum flexibility
- Cost-efficient high-mix/low-volume production
- Short development cycles with quick process customization for greater production efficiency
We optimized the dimensions of our parts, as well as their weight and stability, while also integrating functionality directly into them – all in the same part. Thanks to the reliability and precision that we achieved, special police and military units throughout Europe are now using our lamp.
Hagen Tschorn | Managing Director | canto Ing. GmbH & THOR offshore engineering GmbH