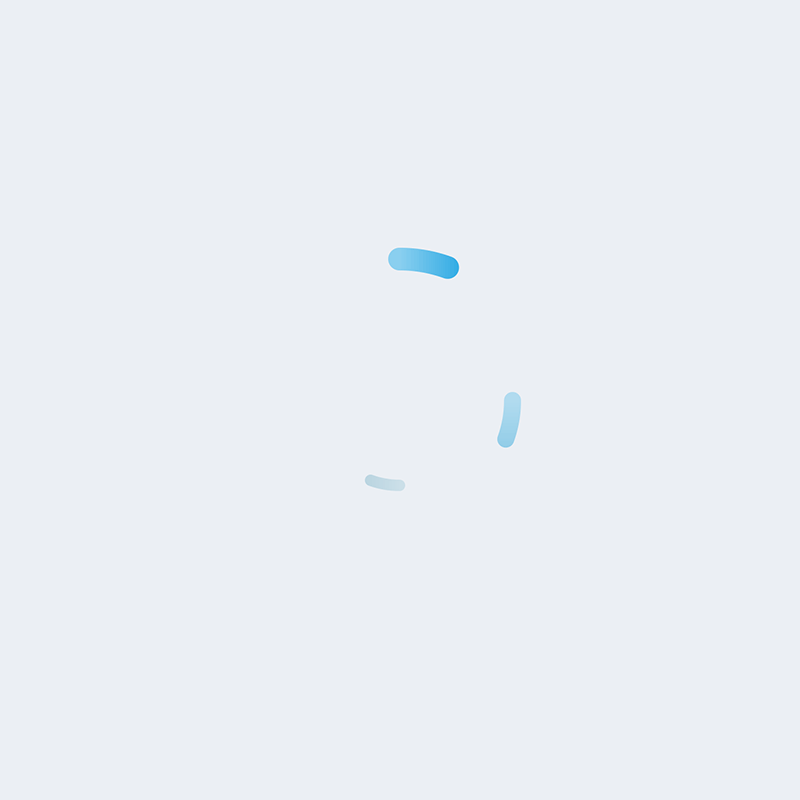
3D ceramic printing
From industry to medicine and beyond. With Lithoz 3D printers and premium materials, previously unimaginable projects become real.
How does it work?
Lithoz's LCM technology makes it possible to produce even the most complex geometries and miniaturized structures, enabling designs that are unattainable with conventional ceramic processes.
The powerful LCM process developed by Lithoz has already enabled the production of many innovative applications that meet or exceed the mechanical performance and reproducibility of ceramic components produced by conventional methods.
When it comes to absolute accuracy, high resolutions and complex structures, LCM technology is your clear first choice.
1.
Starting with a CAD model, the first step in the LCM process is work preparation and design optimization. The information for the print job is digitally transferred directly from your computer to a Lithoz CeraFab 3D printer.
2.
The ceramic-loaded liquid (slurry) is automatically dispensed and applied to a transparent vat. The movable build platform is dipped into the slurry from above before being selectively exposed to visible blue light from below the vat. Each layer image projected onto the slurry is produced via a digital micromirror device (DMD) in combination with a state-of-the-art projection system. By repeating this process, a three-dimensional green part can be created layer by layer.
3.
After thermal post-processing, the binder is removed and the components are sintered, resulting in fully dense ceramic components. LCM technology utilizes decades of experience in processing ceramic powders. By using the same powders and ovens as injection molding, ceramic components with excellent mechanical properties and surface qualities can be 3D-printed.
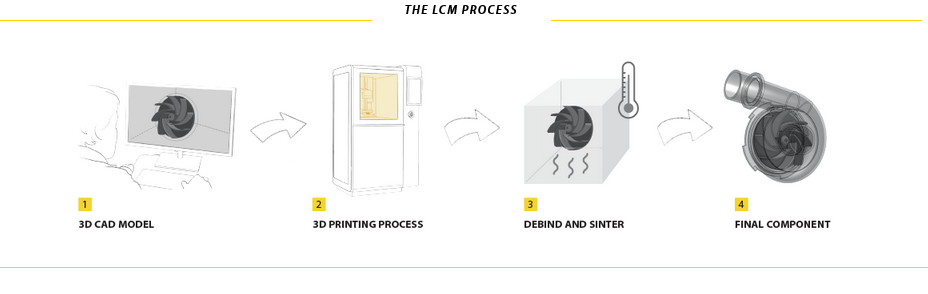
Advantages of printing on ceramics
Pevnost a kvalita
tištěného dílu
Strength and quality of the printed part
Úspora času
Achieving
complex details
Saving time
Saving finances

Additive Manufacturing in Motor Sports
Faster, lighter – and always safe: these are the requirements of motor sports development. For decades, EOS has been working with customers to exploit new potential using industrial 3D printing.
More information →
Additive Manufacturing for Serially Produced Vehicles
We help our customers implement additive manufacturing wherever it can fully demonstrate its strengths. This ranges from major changes to logistics systems, detailed equipment customization and lightweight parts, to engine technology fine-tuning. 3D printing technology holds the potential to optimize the automotive production value chain and react quickly and flexibly to new trends. This potential is extremely valuable in an industry where every player, automotive manufacturer, OEM and tooling provider faces high costs and innovation pressure.
More information →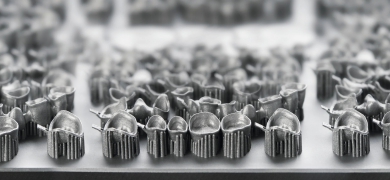
3D Printing of Bridges, Crowns and More
Partial dentures need to fit the patient without any compromise, as well as looking natural and aesthetic. Ideally, they should also last forever. Bridges, crowns and model cast prostheses are usually manufactured by hand – a complex and cost-intensive process.
More information →