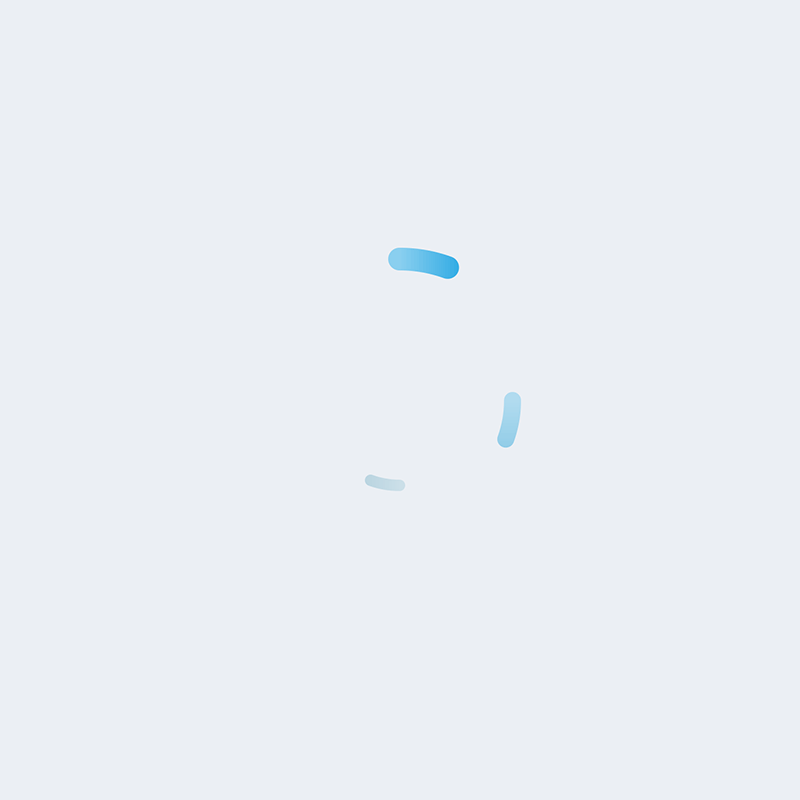

EOS P 500
Plastic Laser Sintering on Industrial Scales
Build rate of up to 6.6 l/h with a packing density of 5%
Lowest price per part on the market
Automation-friendly platform with standardized software interfaces
Reduced Costs
The innovative layering system, which applies and compacts the material at up to 0.6 m/s, and the two powerful 70-watt lasers reduce the costs per part by more than 30%.
Diversity of Materials
The system processes high-performance plastics, enabling maximum diversity of materials. Application and material development are supported by open software interfaces and user-friendly tools.
Automation
The system is intuitively controlled by EOSYSTEM. Software integration in CAD systems, e.g. NX™ by Siemens, is provided by EOSPRINT 2, and a connection to ERP systems is provided by EOSCONNECT. Automated interfaces and optimized accessories reduce the cycle time and guarantee operational build times lasting several days.
Technické údaje EOS P 396
- Construction Volume
- 500 x 330 x 400 mm (19.7 x 13 x 15.7 in)
- Laser Type
- CO₂, 2 x 70 W
- Precision Optics
- F-theta lens, surface module, high-speed scanner
- Scan Speed
- up to 2 x 10 m/sec (32.8 ft/s)
- Power Supply
- 400 V / 100 A; max. power consumption 80 A
- Machine Dimensions (W x D x H)
- 3,400 x 2,100 x 2,100 mm (133.9 x 82.7 x 82.7 in)
- Recommended Installation Space
- min. 7.2 x 5.2 x 4.2 m (284 x 205 x 165 in)
- Weight
- approx. 7,000 kg (15,432 lb)
- Software
- EOSYSTEM with EOSAME feature, EOSPRINT 2 with SmartScaling feature and EOS ParameterEditor, EOSCONNECT Core, EOSCONNECT MachinePark, EOSTATE Powderbed

Additive Manufacturing for Handling Systems
Automation is moving forward, and all types of production and intralogistics processes are becoming increasingly networked thanks to digitalization. Robotics and gripping systems play a key role in this. But gripping technology in particular is constantly facing new challenges. Additive manufacturing makes it possible to address rapidly changing market trends in a targeted manner.
More information →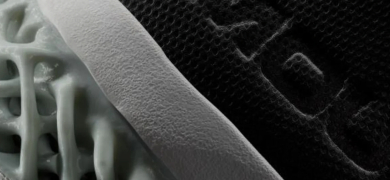
Additive Manufacturing for a Perfectly Fitting Shape
Personalization has been more than just a trend for a while now. As well as offering greater comfort to their wearers, custom shoe soles open up completely new possibilities for fashion customization.
Additive manufacturing has the solution: Thanks to a fully digital process, trendy designs can be put together using scans of the sole of the foot, then transformed into custom-fitting shoe soles made from polymer materials by industrial 3D printing.
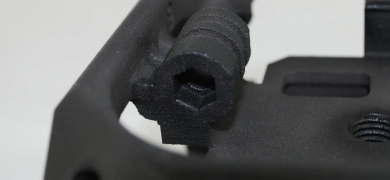
Housings for Electronic Components
Having a stable housing protects the interior. Robust cases are often essential, especially for sensitive electronics. They need to be strong and properly sealed, while also fitting as closely as possible, and they need to be manufactured quickly enough to achieve short production cycles. However, with the injection molding process, manufacturing housings with these properties is only viable in very large series productions.
More information →